How to Effectively Clean and Test Your Cold Storage System
In the intricate world of cold storage installations, ensuring the system's optimal performance post-setup is paramount. This entails meticulous preparation and rigorous testing procedures to prevent operational failures and maintain the system's longevity. From cleaning debris to conducting pressure and leakage tests, each step guarantees the efficient operation of quick-frozen cold storage units. This guide outlines the crucial phases involved in preparing and testing cold storage systems, providing a detailed look into the practices that ensure their reliability and efficiency.
① System sewage: as a result of the cold storage installation and the management of machine and equipment materials, the system exists within the welding slag, oil stains, dust, and even gauze head and other dirt will inevitably affect the future operation of the quick-frozen cold storage. So, it is necessary to use high-pressure gas to blow clean the debris in the system. Generally, a large caliber for a large amount of sewage can be chosen; dirt falling on the bottom of the container can choose a low position at the discharge. System sewage results in the sewage outlet on the white cloth board being completely free of grease and dust marks before the system is considered clean. Drainage should pay attention to keeping the automation components clean and undamaged after the discharge of each filter is re-cleaned (including the main valve parts).
② System pressure test: high-pressure part of the 18MPa air pressure test; low-pressure part of the 16MPa air pressure test.
③ Host debugging: In the absence of a high-pressure air compressor, the available refrigeration machine is used instead of an air compressor for the system pressure test, so the debugging host is usually used.
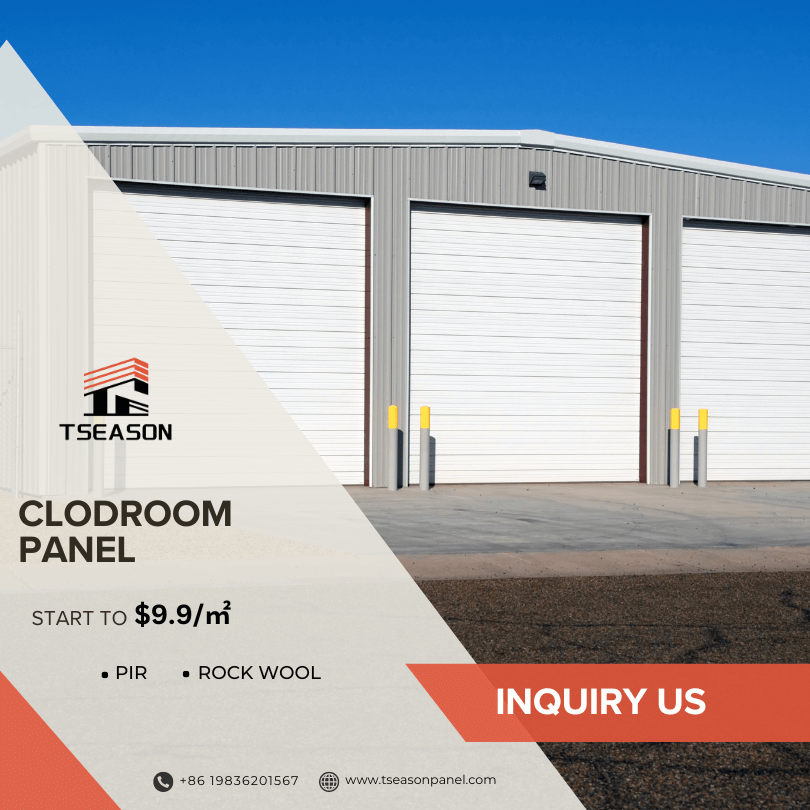
④ System leakage test: the first air pressure test leakage detection, generally can be coated with soapy water for leakage cluster check, found that the leakage is well marked, to be removed after the pressure to make up for the weld, generally only allowed to make up for the weld twice, such as the leakage of the place again, it must be cut off this section of the pipe to reweld until all the non-leakage. After checking, you can put a small amount of refrigerant into the system and then pressurize it with air, use phenolphthalein test paper to check the leakage of ammonia and use a leakage detection lamp to check the leakage of the Freon system.
⑤ Remove water in the system: The Freon system must still be cleaned with high-pressure nitrogen to remove water or water vapor in the Freon system. Even so, it is necessary to put silica gel in the drier of the Freon system. In the test run, the silica gel color reduction, such as moisture, must be dried silica gel or new silica gel if the system is found to be more moisture, but also with calcium chloride in time to change out until the Freon system without moisture or only a minimal amount of water to prevent ice blocking phenomenon, affecting the regular operation of the equipment after the installation of the cold storage.
⑥ System test vacuum: Vacuum the system and static pressure when the system vacuum degree reaches 650mm (1mmHg=9.80665Pa) and keep the pressure not rising within 12h as qualified.
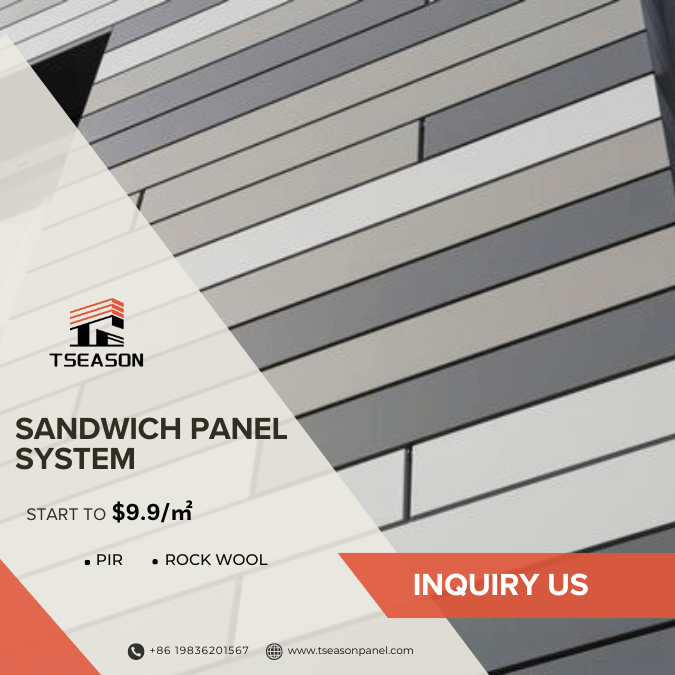
Ensure that the whole cold storage system is entirely non-leakage, and then the equipment, pipeline insulation, heat preservation, air, and moisture insulation, and paint before the system refrigerant filling and system test run in the cold storage installation of the whole system gradually after the adjustment.