Maximizing Efficiency with Composite Sandwich Panels: Insights into Bending Loads
Composite Sandwich Panels
A sandwich panel is a composite construction material consisting of two outer layers (called facings) and a lightweight core material sandwiched between them. The facings are typically made from materials such as metal, plastic, or composite materials, while the core can be made from various materials, including foam, honeycomb, or other lightweight structures. This design provides a high strength-to-weight ratio, thermal insulation, and excellent soundproofing properties.
Sandwich panels are widely used in various applications, including:
- Construction: For walls, roofs, and floors in commercial and industrial buildings.
- Transportation: In vehicle bodies, trailers, and ships to reduce weight while maintaining strength.
- Aerospace: In aircraft components to achieve lightweight yet strong structures.
- Furniture: In lightweight furniture designs that require durability.
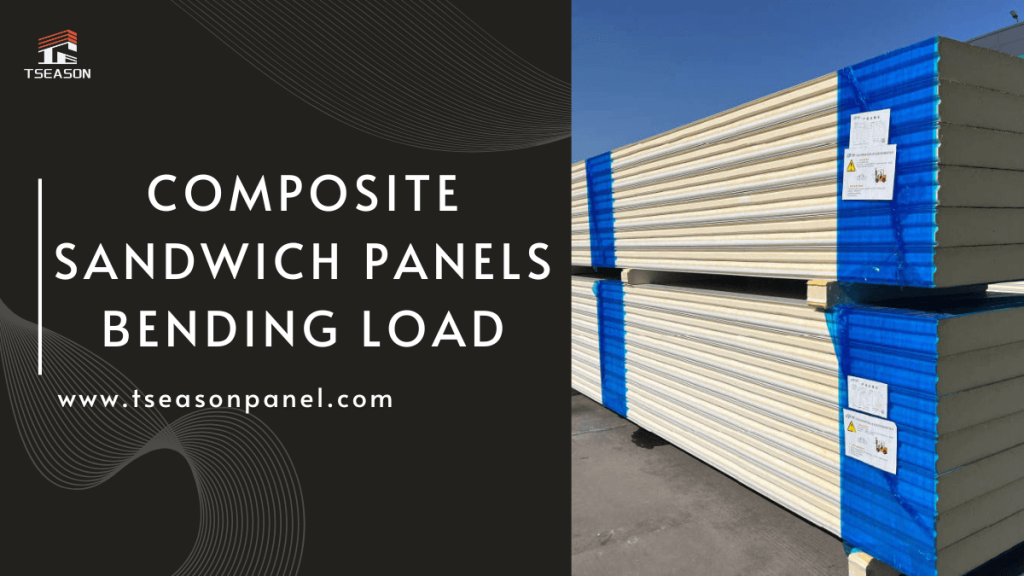
I. Bending Test
There are three common types of tests: two-point bending, three-point bending, and four-point bending. Composite materials and wood typically use the four-point bending test. This test requires a deflectometer to accurately measure the deflection of the sample at the center of the support span. The test results are the same as those of three-point bending, including bending strength and bending modulus.
II. Bending Strength
Bending strength refers to the strength of the material at the point of failure under bending loads, reflecting the material's resistance to bending. Bending modulus indicates the stiffness of the material under bending loads, reflecting its ability to deform.
III. Testing Method
- Test Purpose
- To determine the bending strength and bending modulus of composite sandwich panels under bending loads.
- Testing Equipment
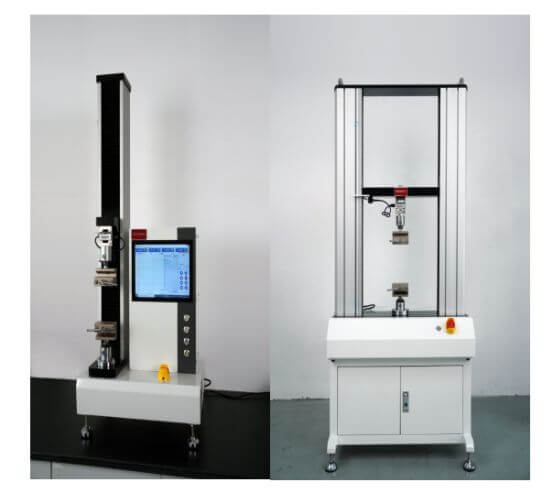
IV. Testing Procedure
- Sample Preparation: Prepare composite sandwich panel samples that meet standard requirements. They are typically in a rectangular shape and processed to specified dimensions according to standards.
- Testing Equipment Preparation: Install the bending testing equipment and calibrate it to ensure it meets standard requirements.
- Test Parameter Settings: Set test parameters according to standard requirements, such as loading speed, loading method, loading position, and test temperature. These parameters may vary based on different standards.
- Test Operation: For strength determination, place the sample on the supports of the bending test, apply the loading head, and insert a hard rubber pad between the head and the sample. Adjust the zero point of the testing machine, and uniformly load it until the sample fails, recording the failure load and observing the failure mode.
- Stiffness Measurement: Apply a preload (15% to 20% of the failure load) to eliminate any gaps between the sample and the supports, then reduce it to the initial load (5% of the failure load). Adjust the zero point of the instrument, then use 5% of the failure load as the range and load up to 40% to 50% of the failure load in steps, recording each load and the corresponding deflection values. If the entire load-deflection data is required, testing should continue until failure. If an automatic recording instrument is available, loading can be continuous.
- Data Recording and Analysis: Record test data such as loading force, sample deformation, and test duration. Calculate the bending strength and bending modulus based on the test data, and perform data analysis and statistics.
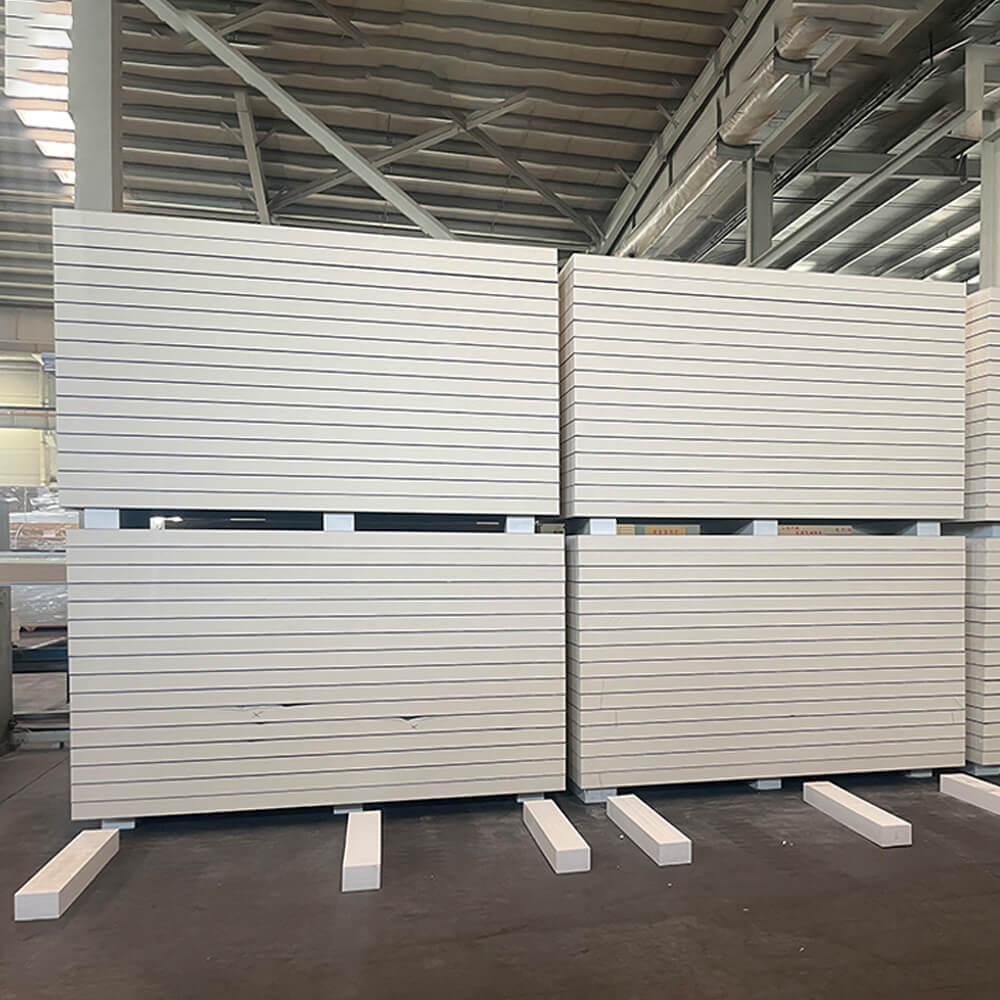