Optimizing Energy Efficiency in Cold Storage Refrigeration Systems
Analyzing and optimizing refrigeration systems in the cold storage industry can reduce energy costs and enhance economic efficiency for enterprises. Here is a structured approach to efficient system preparation and operation.
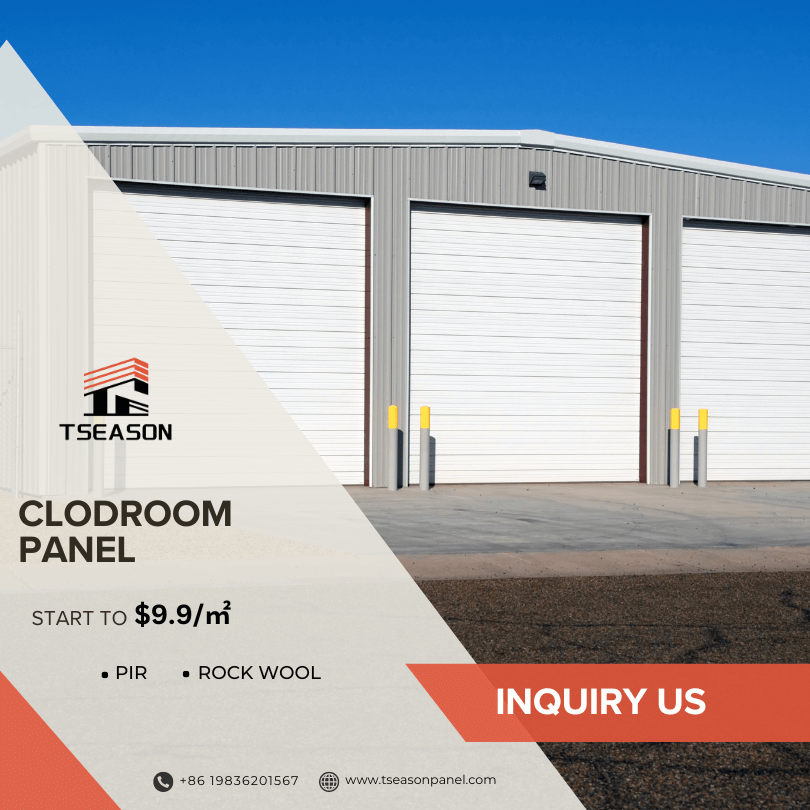
1. System Cleaning
To prevent operational issues, remove contaminants like welding slag, oil stains, and dust from the system using high-pressure gas. A large-diameter pipe ensures thorough wastewater discharge, and all components should be cleaned post-drainage. Automation parts should remain clean and intact throughout the process.
2. Pressure Testing
Conduct specific pressure tests for different sections: high-pressure parts use 18 MPa air, while low-pressure parts are tested with 16 MPa air.
3. Main Unit Commissioning
In cases without a high-pressure air compressor, the refrigeration unit can be used for pressure testing.
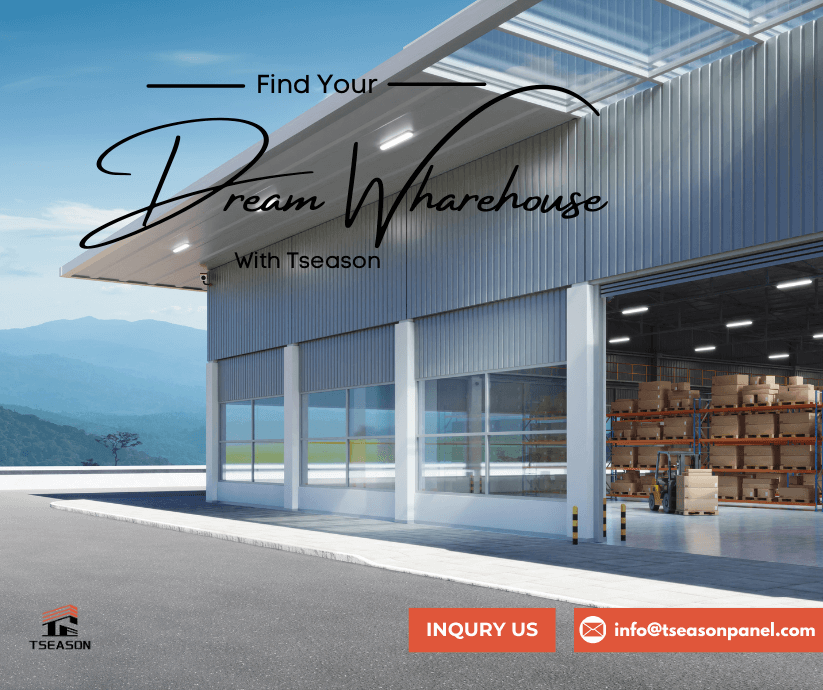
4. Leak Testing
Leak testing involves using air pressure and soapy water to locate any leaks. Repairs are allowed up to twice; if additional leaks occur, re-welding is required. Phenolphthalein test paper is used for ammonia leaks, while Freon systems employ a leak detector.
5. Water Removal
In Freon systems, high-pressure nitrogen helps remove water, with silica gel added to the dryer for moisture absorption. If excess moisture persists, replacing the silica gel with calcium chloride may be necessary to prevent ice blockage.
6. Vacuum Testing
A vacuum test ensures the system’s airtightness. The system is considered secure when vacuum levels reach 650 mm Hg and hold for 12 hours without a pressure increase.
After verifying airtightness, apply insulation and protective paint to all equipment and pipes before filling the system with refrigerant. Finally, run a complete system test, adjusting as necessary for efficient operation.