What Is A Prefab House?
Introduction
The term 'prefab' is a sweeping concept in contemporary home building, encompassing a wide range of approaches without pinpointing anything specific. This versatility can be perplexing, given the myriad methods falling under the 'prefab' umbrella. In this exploration, we aim to demystify the terminology, examining its meanings, allure, limitations, and our stance within this expansive field.
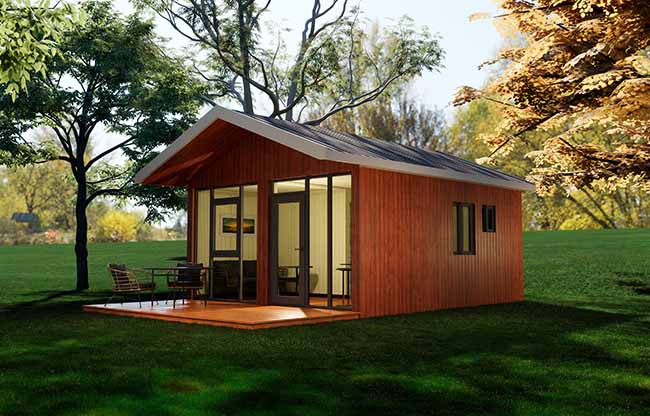

What is a Prefab Home?
Prefabricated houses, commonly known as prefab homes, earn their name from being primarily manufactured off-site before being delivered and assembled on-site. In the UK, prefabs historically suffered from a negative reputation, associated with low-quality, mass-produced housing replacing structures destroyed during World War II. Despite initial intentions for temporary use, some prefabs endure today, showcasing the longevity of these structures.
While a stigma still lingers, contemporary prefab homes are now synonymous with quality and efficiency. The term 'prefabrication' loosely translates to 'made before,' a concept embedded in traditional house-building methods, where components like timber roof trusses were crafted off-site. Today, the term 'prefab' blankets various modern construction methods, leading to its widespread usage. Any home can be deemed prefab if some part of it is constructed before arriving at the site.
Three terms often used interchangeably with 'prefab' are modular, volumetric, and kit homes, each representing subcategories with distinct characteristics.
Modular Homes: Building Blocks of Innovation
Modular homes are constructed in large sections, resembling a colossal Lego set. Notable prefab companies, such as Baufritz, prefabricate entire wall sections in factories, which are then craned into place on site. Despite the swift assembly of the building envelope, considerable work remains for the interior fit-out, extending the construction timeline. Challenges like flatlining productivity, build quality concerns, and high costs have been associated with modular construction.
Volumetric Homes: Beyond Traditional Boundaries
Volumetric modular manufacturing involves prefabricating larger, fully finished elements in factories. These 'modules' include pre-fitted components like electrics, plumbing, heating, doors, windows, and internal finishes. Commonly used for larger developments, volumetric homes boast high standardization and rapid on-site assembly. However, they may be less suitable for individual customers due to challenges in finding sites that align with standardized designs.
Kit Homes: Empowering Individual Builders
Kit homes, or self-build 'kit homes,' are delivered flat-packed for assembly by contractors or even the homeowners themselves. This option encourages hands-on involvement, allowing individuals to manage or construct their homes. Kit house companies, like HebHomes, offer various packages, from building envelopes to complete home kits.
Why the Prefab Interest?
Despite interchangeable use of terms like 'prefab,' 'modular,' 'kit,' and 'volumetric,' a growing number of UK residents are considering prefab for home construction. While not a new concept, advanced prefabrication techniques now offer significant benefits. Modern prefab homes assure customers of cost certainty, fixed timelines, quality guarantees, and enhanced environmental performance. The faster overall construction program is a compelling factor, reducing stress levels for aspiring self-builders.
Challenges of Prefabrication
The conventional notion of prefab homes, primarily modular or volumetric, is hailed as the future of house building due to mass, factory-based production efficiency. However, some limitations arise when applied to individual homes:
1. Quality Concerns
Calling something prefab doesn't guarantee superior craftsmanship; manual skills on production lines still play a vital role.
2. Design Limitations
Factories often produce standardized products, limiting overall design options available to customers.
3. Logistical Challenges
Delivering large components to sites can pose logistical challenges, especially when crane access is restricted.
4. Lead Time
Production time in the factory adds to the overall construction timeline despite shorter on-site work periods.
5. Higher Costs
Factories with constant output needs may charge customers more due to overheads.
The Future Beyond Prefab
While prefab remains a relevant discussion, we believe that digitizing the process is the next step for the home building industry. Facit Homes, recognized for its innovation in prefab housing, aligns more with modern car manufacturing principles. We leverage digital manufacturing technology to ensure high-quality, bespoke homes while maintaining flexibility for individual designs. Our approach, akin to 'just in time' assembly, optimizes prefabrication elements for superior performance.
Regardless of precise categorization, we prioritize prefabrication elements to create top-tier, tailored homes. If these homes are best described as 'prefab,' we gladly embrace the term.
Facit Homes: Pioneering the Future of Home Construction